刻蚀工艺概述及应用
1. 引言刻蚀工艺(Etching Process)是半导体制造中至关重要的步骤之一,广泛应用于集成电路(IC)、微机电系统(MEMS)和光电子器件等领域。其核心目的是通过去除硅片表面覆盖的特定材料,实现精确的图案化和微结构加工。刻蚀工艺通常配合光刻技术使用,确保器件的尺寸和形貌符合设计要求。
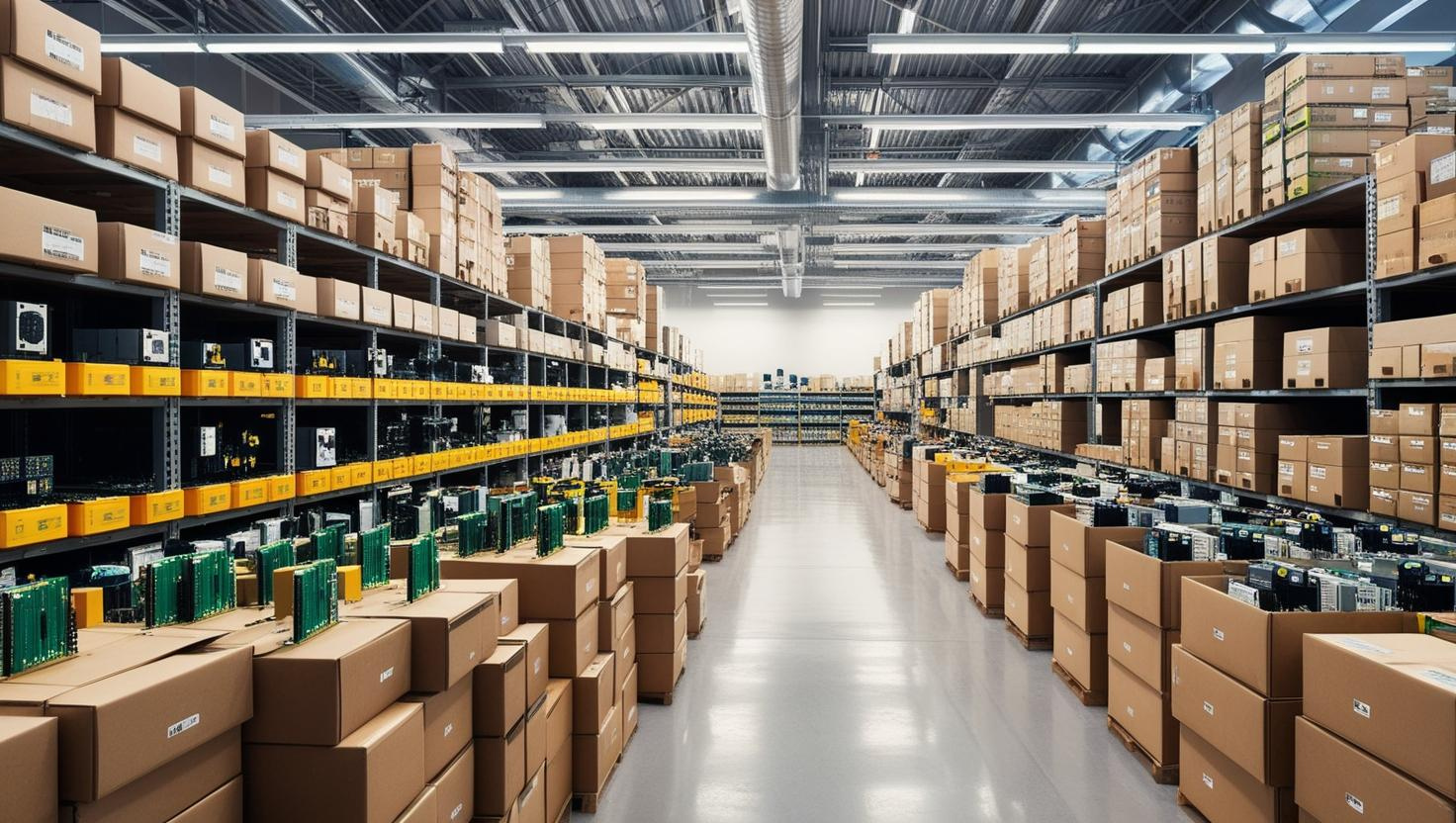
2. 刻蚀工艺流程刻蚀工艺通常包括以下几个主要步骤:
2.1 预处理在刻蚀前,需要对硅片进行严格的清洁,包括去胶、去除颗粒和氧化层,以确保表面无污染,提高刻蚀的均匀性和重现性。
2.2 光刻胶涂覆在硅片表面均匀涂覆光刻胶后,使用光刻工艺将所需图案转移至光刻胶层,以保护部分区域免受刻蚀。
2.3 显影经过曝光后的光刻胶通过显影剂处理,去除未曝光或已曝光的部分(正胶或负胶),露出待刻蚀区域。
2.4 刻蚀使用适当的刻蚀技术(湿法或干法)去除暴露区域的材料,形成所需的结构和图案。
2.5 清洗刻蚀完成后,对样品进行清洗,去除残留的光刻胶和刻蚀副产物,为后续工艺提供干净的表面。
3. 刻蚀工艺的分类根据刻蚀方式的不同,刻蚀工艺主要分为湿法刻蚀和干法刻蚀。
3.1 湿法刻蚀(Wet Etching)湿法刻蚀利用化学溶液与材料发生反应,溶解目标材料并去除,常用于金属材料和有机薄膜的刻蚀。
优点:刻蚀速率快,适用于大面积加工。
缺点:各向同性刻蚀,导致侧向腐蚀,影响精度。
3.2 干法刻蚀(Dry Etching)干法刻蚀利用等离子体或反应气体对材料进行物理或化学去除,适用于高精度和高深宽比结构的加工。
优点:各向异性强,能实现垂直侧壁刻蚀。
缺点:设备复杂,成本较高。
4. 影响刻蚀工艺的关键因素4.1 刻蚀气体刻蚀气体的种类直接影响刻蚀速率和表面质量,如:
氧气(O₂):用于光刻胶去除。
氟化气体(CF₄、SF₆):常用于硅刻蚀。
氯气(Cl₂):适用于金属刻蚀。
4.2 刻蚀机参数刻蚀机的功率、腔体压力、气体流量和温度等参数会影响刻蚀的均匀性和速率,需要优化调整以满足特定工艺需求。
4.3 刻蚀时间刻蚀时间决定了材料的去除深度,需要精准控制,以防止过度刻蚀或刻蚀不足。
4.4 刻蚀选择性选择性是指刻蚀剂对不同材料的作用程度。高选择性意味着刻蚀剂只作用于目标材料,而不会损伤其他部分,从而提高加工精度。
4.5 刻蚀剂浓度刻蚀剂的浓度影响刻蚀速率和刻蚀质量,需要根据材料特性进行优化。
5. 刻蚀工艺的应用刻蚀工艺在现代微电子制造中有广泛应用,主要包括:
5.1 半导体芯片制造刻蚀用于形成晶体管栅极、电路互连等微观结构,实现集成电路的功能。
5.2 MEMS器件加工MEMS器件需要高精度的微结构,刻蚀工艺可用于微传感器、微执行器等器件的制造。
5.3 光电子器件制备光电子器件(如激光器、光波导等)需要精确的图案化加工,刻蚀工艺提供了高分辨率和良好的控制能力。
6. 结论刻蚀工艺是半导体制造中不可或缺的技术,通过合理选择刻蚀方法、优化工艺参数,可实现高精度的微纳加工。未来,随着半导体工艺向更先进的节点发展,刻蚀工艺将在提升制造精度、降低生产成本方面发挥更大作用。