贴片电阻(SMD电阻)广泛应用于电子产品的设计与制造中,其焊接质量直接影响着电路的性能与稳定性。掌握贴片电阻的焊接方法对于确保产品的质量至关重要。本文将为您详细介绍贴片电阻焊接的七大步骤,并分析每个步骤的重要性,以帮助工程师与技术人员提高焊接质量,减少故障率。
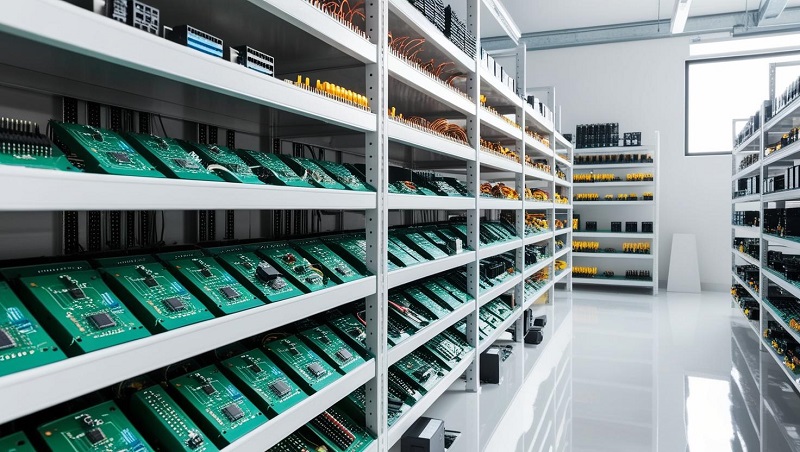
1. 准备工作:清洁和检查
在进行贴片电阻焊接前,首先要确保所有焊接设备、材料和PCB板(印刷电路板)处于良好的工作状态。清洁工作是焊接成功的基础。
1.1 清洁工具与材料
烙铁及焊接设备:检查烙铁的温度是否稳定,焊锡是否充足,焊接工作台的工具是否清洁且齐全。
焊接环境:确保焊接台面没有灰尘、油污或其他杂质。可以使用无尘布或纸巾进行清洁。
电阻元件与PCB板:检查贴片电阻是否有损坏,确认电阻的型号与PCB板上的焊接位置是否匹配。若电阻表面有污垢或氧化,应使用酒精或专用清洁剂清洁。
1.2 检查焊接材料
焊锡丝是焊接过程中的关键材料,确保焊锡质量符合要求,避免使用已经受潮的焊锡丝。同时,建议选择带有助焊剂的焊锡丝,这可以有效减少焊接时的氧化问题。
2. 贴片电阻定位
贴片电阻的准确定位对于焊接的成功至关重要。在贴片电阻的放置过程中,必须保证其与PCB板上的焊盘对齐,以便完成精准的焊接。
2.1 使用贴片机或手工放置
在批量生产中,常使用自动贴片机将电阻元件准确放置在PCB板上。对于小批量或修复工作,可以使用镊子手工放置电阻。此时,确保电阻与焊盘之间的接触良好,避免因位置偏差导致焊接不牢。
2.2 检查放置位置
使用显微镜或放大镜仔细检查电阻的放置位置,确保其与焊盘完全对接。如果发现位置不正确,应及时调整。
3. 涂抹助焊剂
助焊剂是焊接过程中的重要辅料,它有助于去除金属表面氧化物,保证焊接处的良好连接。
3.1 选择合适的助焊剂
市面上有多种类型的助焊剂,其中水溶性助焊剂、无清洗助焊剂和有清洗助焊剂是常见的选择。水溶性助焊剂清洁后可保持表面无残留,而无清洗助焊剂则能在焊接后减少清洁工作。
3.2 涂抹助焊剂
使用助焊剂时,需均匀涂抹在焊盘上,并确保焊盘表面湿润。涂抹过多的助焊剂可能会导致焊点不清晰,影响后续焊接过程中的质量。
4. 焊接温度与时间控制
焊接温度的控制对于确保焊点的质量至关重要。过高或过低的温度都会影响焊接的效果,导致焊点不牢固或焊接缺陷。
4.1 温度控制
在使用烙铁进行焊接时,推荐的温度范围通常为350°C左右,具体温度应根据焊锡丝和PCB板的材料来调整。过高的温度可能会导致PCB板和元件受损,过低的温度则可能使焊接不完全。
4.2 焊接时间控制
焊接时间的长短应根据元件的焊接难度来决定。通常,焊接时间不应超过3秒,以防止元件过热。在焊接过程中,可以通过观察焊锡的熔化情况来判断焊接时间是否合适。
5. 焊接操作
焊接操作是整个焊接过程中的关键步骤,要求操作人员具备一定的技巧和经验。
5.1 使用烙铁进行焊接
将烙铁的尖端轻触焊盘和电阻的引脚,稍等片刻,待焊锡熔化后再进行焊接。确保焊锡能够完全流入焊盘与电阻引脚之间,形成良好的焊点。
5.2 焊接技巧
避免直接将烙铁尖端与电阻的引脚接触过久,以防过热。
焊接过程中应保持烙铁与元件引脚、焊盘的接触时间一致,防止出现冷焊或假焊。
如果焊点过多,可能会出现短路现象,因此应控制焊锡的使用量。
6. 检查焊点质量
焊接完成后,必须进行质量检查,以确保每个焊点牢固且符合标准。
6.1 焊点检查方法
使用显微镜或放大镜仔细检查每个焊点,确认焊点表面光滑、无裂纹,且与焊盘的接触良好。若出现虚焊、冷焊或短路现象,应立即进行修复。
6.2 焊点的电气性能检查
通过测试设备检查每个焊点的电气性能,确认没有短路、开路或焊接不良的情况。此步骤对于确保电路的正常运行至关重要。
7. 清洁和后处理
焊接完成后,必须清理焊接表面,以去除多余的焊锡残留物和助焊剂,确保电路板的干净和电气性能的稳定。
7.1 清洁焊接区域
使用无尘布蘸取适量的清洁剂,轻轻擦拭焊接区域,去除焊接过程中的助焊剂残留物。清洁时要注意避免损坏电路板或元件。
7.2 后处理检查
完成清洁工作后,再次使用显微镜进行检查,确保焊接区域无污染物,并确认焊接效果符合质量要求。
结语
贴片电阻的焊接是电子产品制造中的一个重要环节,其焊接质量直接影响到产品的电气性能与稳定性。通过以上七个步骤的详细介绍,我们可以看到每个环节都至关重要。从前期的准备工作到最终的清洁与检查,每一步都需要细致入微的操作。掌握正确的焊接技巧,可以有效减少焊接缺陷,提升焊接质量,保证电子产品的长期稳定运行。